HENRY BEGUELIN
A STORY OF UNIQUE CRAFTMANSHIP
Born on the island of Elba in the early ‘80s, Henry Beguelin began as an artisanal experiment among friends, crafting distinctive leather goods from natural and recycled materials. What started with belts soon expanded to bags, shoes, furniture, and apparel—always maintaining a commitment to tradition, quality, and uniqueness. The signature stick figure, hand-stitched in waxed thread, remains a mark of authenticity and craftsmanship.
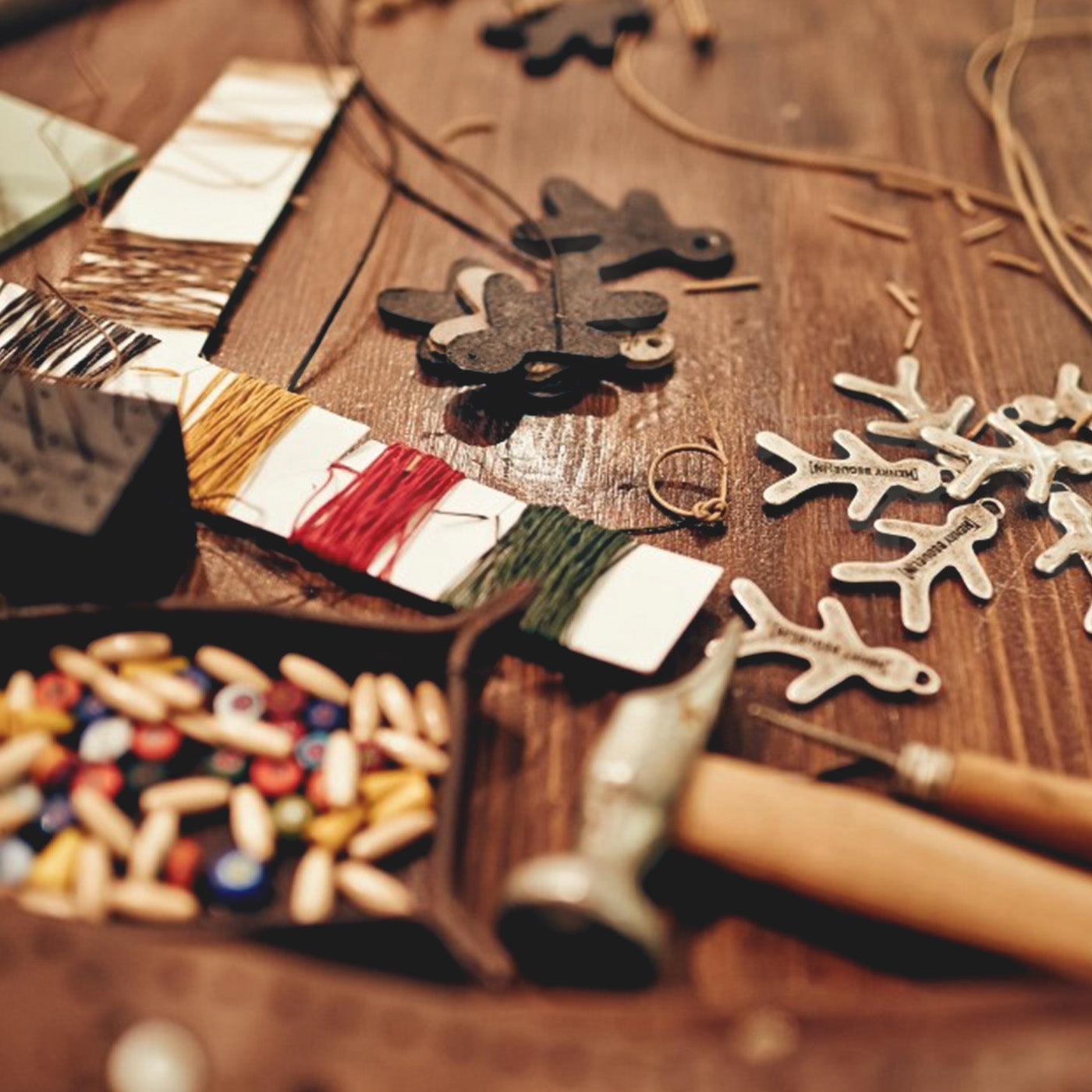
HANDMADE
ONE OF A KIND
Every Henry Beguelin piece is meticulously handcrafted using traditional techniques passed down through generations. Skilled artisans use time-honored tools—awls, engraving machines, and hand-sewn waxed threads—to create products that are truly unique, celebrating imperfections as a hallmark of individuality and artisanal excellence.
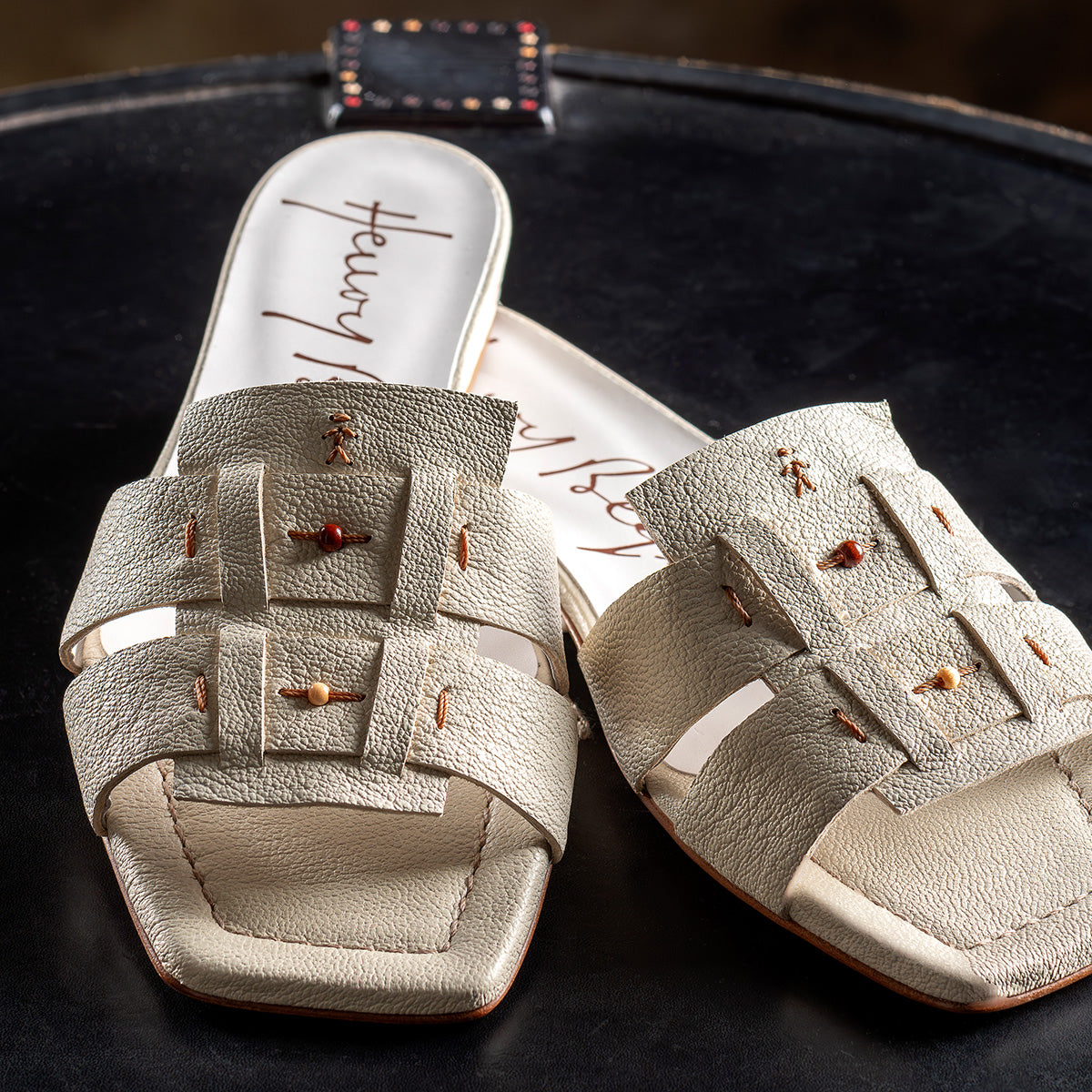
The Art of Stitching & Decoration
Stitching is at the heart of Henry Beguelin’s identity. From strong saddle stitches to decorative beading with Venetian murrine, every detail is carefully crafted. These hand-applied embellishments make each piece one of a kind, blending heritage with artistic expression.
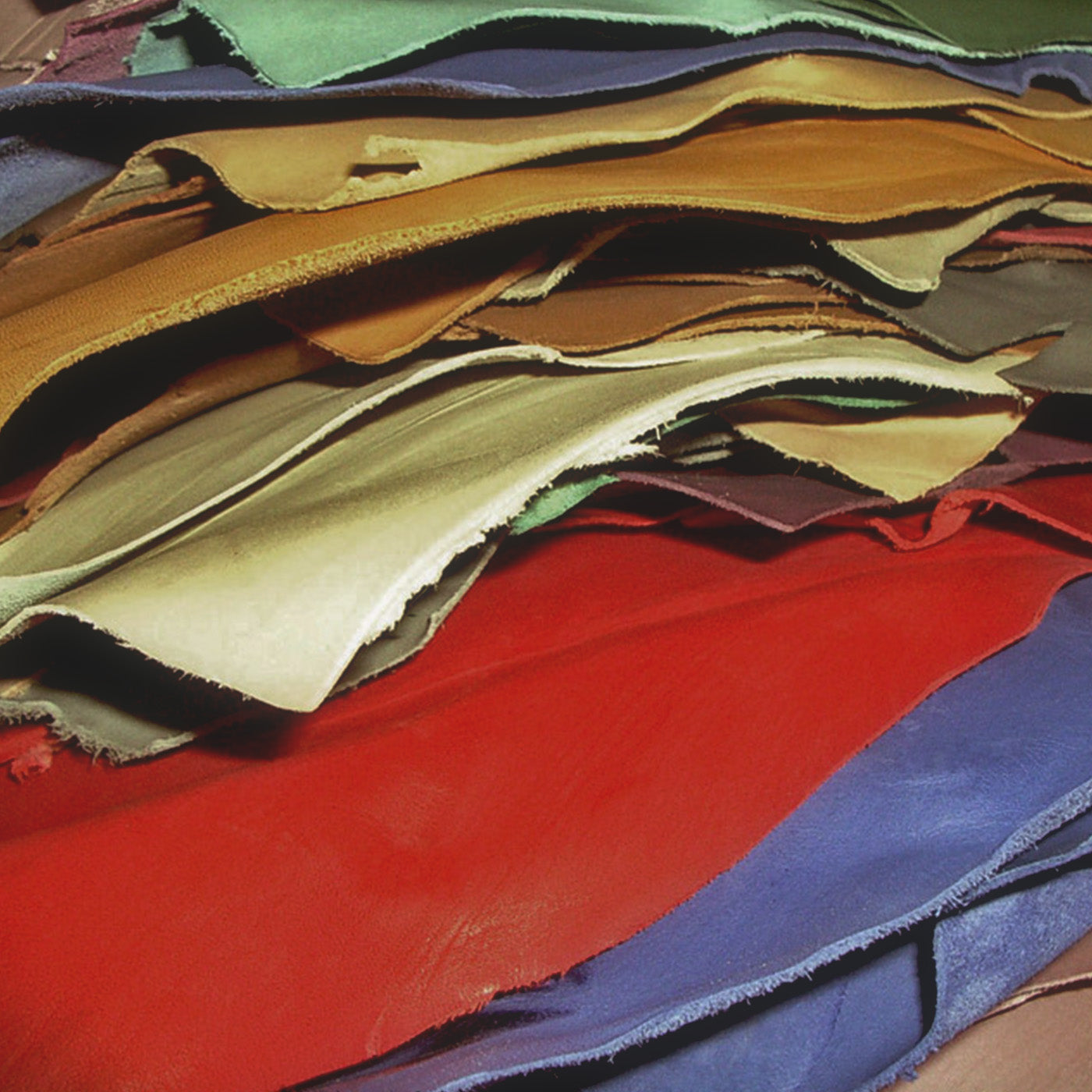
Natural Leather, Timeless Tradition
Our leather undergoes a meticulous tanning and dyeing process, free from aggressive chemicals, preserving its natural character and soft texture. Using time-honored methods, we enhance the organic beauty of each hide while ensuring durability and sustainability.